Hoe zero-defectproductie realiseren bij HVAC-kabelassemblage: best practices
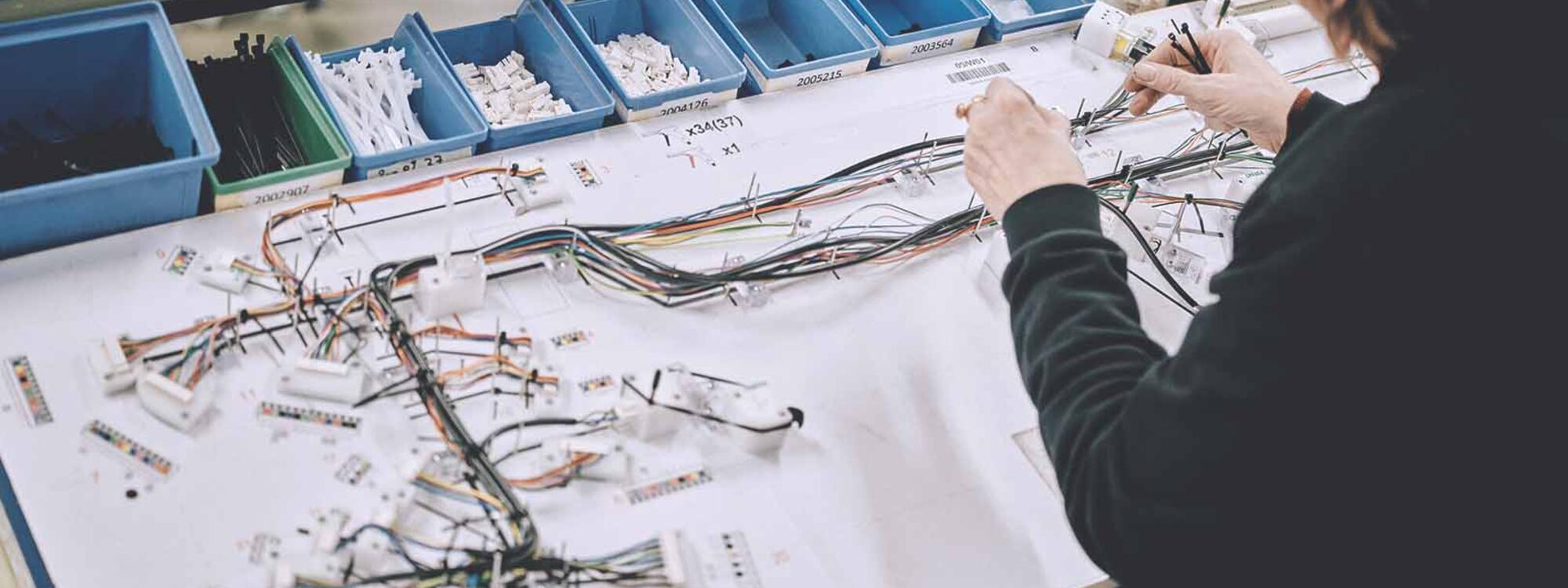
De HVAC-markt is steeds competitiever en meer op kwaliteit gericht. Producten zoals warmtepompen, airconditioningsystemen en (WTW-)ventilatiesystemen worden alsmaar complexer. In deze context is zero-defectproductie de norm geworden – niet alleen om aan de verwachtingen van klanten te voldoen, maar ook om te voldoen aan de strikte veiligheidsnormen die gelden. Als vaste leverancier voor toonaangevende spelers in de HVAC-industrie begrijpen wij dat het leveren van kabels en kabelbomen van topkwaliteit meer vereist dan technische expertise. Het vraagt om een kwaliteitscultuur van continue verbetering en een systematische aanpak om (potentiële) fouten te elimineren. Dit artikel dient als een best-practice case en licht onze aanpak toe hoe men tot een zero-defectproductie kan komen in kabelassemblage, met focus op de belangrijkste principes, uitdagingen en oplossingen.
Wat is zero-defect (kabel)productie?
Zero-defect productie is een kwaliteitsmanagementconcept dat sterk verankerd is in het First Time Right-principe. Het richt zich op het voorkomen van fouten in plaats van ze pas aan te pakken nadat ze zijn opgetreden. Het doel is om de kwaliteit van producten en/of diensten te verbeteren, terwijl de kosten worden verminderd die door fouten en verspilling worden veroorzaakt. De ultieme ambitie van deze filosofie is het creëren van een productieomgeving waarin defecten nagenoeg uitgesloten zijn, waardoor verspilling zoveel mogelijk wordt geminimaliseerd, efficiëntie toeneemt en de klant steevast topkwaliteit ontvangt.
Meer weten hoe u zero-defect kabelproductie kan realiseren?
Download onze gratis whitepaper
Uitdagingen bij het realiseren van een zero-defectproductie in kabelassemblage
Het doel van zero-defectproductie is duidelijk; de weg ernaartoe is echter complex. Bij WAAK hebben we voor het assembleren van kabels en kabelbomen 3 grote uitdagingen geïdentificeerd:
2.1. Beheer van een complex productieproces voor kabels en kabelbomen
Kabel- en kabelboomassemblage bestaat uit een groot aantal opeenvolgende stappen – die elk correct moeten worden uitgevoerd om fouten in het eindresultaat te vermijden. Om deze complexiteit beheersbaar te maken, heeft WAAK de volgende maatregelen ingevoerd:
Samenhangende procesflow
Voor elke kabelboom creëren we een volledig productiedossier. Aan de hand van een stappenschema wordt het logische proces visueel weergegeven. Dit schema toont hoe de kabelboom moet worden samengesteld tot het eindproduct. Deze aanpak zorgt ervoor dat iedereen de individuele stappen en hun onderlinge samenhang begrijpt.
Transparantie van de workflow
Om het werk minder complex te maken en kwaliteitscontrole permanent te waarborgen, delen we de productie op in duidelijk gedefinieerde bewerkingen. Elke bewerking kan meerdere afzonderlijke deelprocessen omvatten, die telkens zijn gedocumenteerd met de volgende kerninformatie:
- Benodigde gereedschappen en materialen
- Specificaties van de werkpost
- Vereist competentieniveau van de operator
- Gedetailleerde procesinstructies
Deze gestructureerde aanpak zorgt ervoor dat we op elk moment het overzicht behouden over de productieflow en dat elk proces transparant en reproduceerbaar is.
Visuele ondersteuning
Tot slot voorzien we voor elke operator visuele hulpmiddelen zoals: schema’s, foto’s en instructiebladen. Deze tools bieden de operator een duidelijke en stapsgewijze begeleiding doorheen het proces.
2.2. Kwaliteitscontrole in kabelproductieproces
Door preventieve maatregelen, duidelijke normen en continue monitoring is kwaliteitscontrole geïntegreerd in elke stap van het productieproces:
Inspectie van inkomende goederen
Voor alle materialen die in het productieproces worden gebruikt, hanteren we een set duidelijke specificaties die bij levering worden gecontroleerd. Als de materialen aan deze specificaties voldoen, worden ze goedgekeurd en geregistreerd. Zo niet, dan wordt de leverancier verwittigd en worden de materialen geïsoleerd in een aparte opslagruimte.
Controle en vrijgave van gereedschappen
Vooraleer een gereedschap wordt ingezet in de productie, ondergaat het een gecontroleerd vrijgaveproces:
- Er worden testproducten geproduceerd en beoordeeld aan de hand van de specificaties.
- Er wordt een vrijgaverapport opgesteld; goedgekeurde gereedschappen worden visueel gemarkeerd.
- Alle gereedschappen worden onderworpen aan preventief onderhoud om consistente prestaties te garanderen.
FMEA Control Plan
Een essentieel onderdeel van WAAK’s kwaliteitsstrategie is de inzet van Failure Mode and Effects Analysis (FMEA). Deze methodiek helpt ons om:
- Potentiële faalwijzen in producten en processen te identificeren
- De oorzaken en gevolgen van deze fouten te analyseren
- Acties te prioriteren om risico’s te beperken
De resultaten van de FMEA-analyse worden rechtstreeks verwerkt in een gedetailleerd FMEA Control Plan dat het volgende vastlegt:
- Kritieke procesparameters
- Inspectiemethodes en -frequentie
- Concrete acties om de kwaliteit te monitoren en beheersen
Dankzij de FMEA-analyse en het bijhorende controleplan worden risico’s proactief beheerd.
Ontdek meer beproefde strategieën voor het bereiken van zero-defect productie in het volledige artikel:
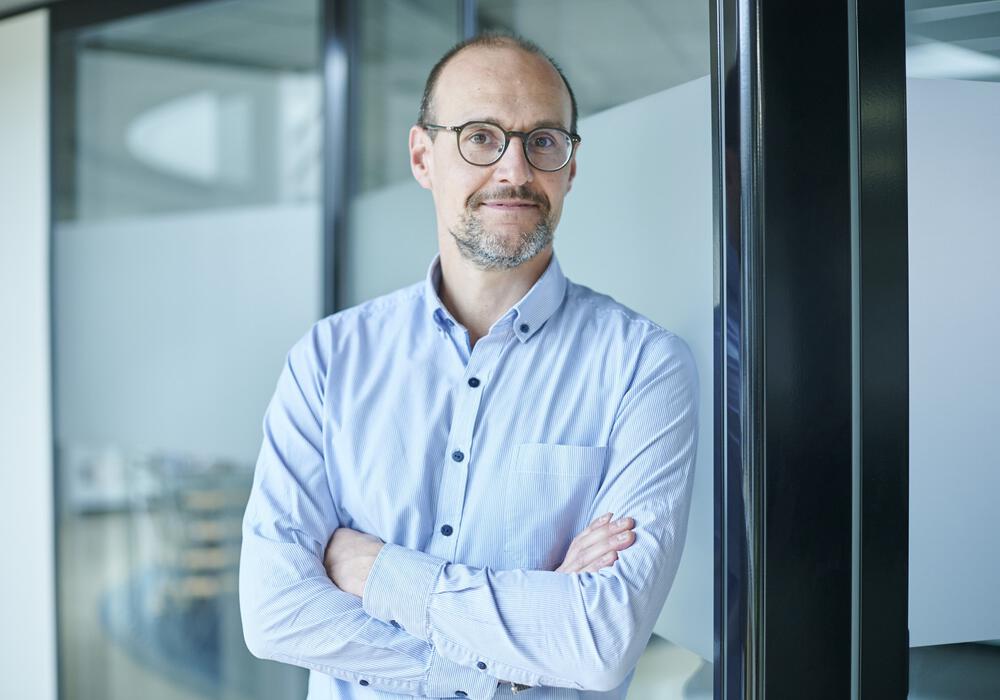
Zoek niet verder, wij hebben alle know-how in huis om u verder te helpen!
Kristof Hots
Directeur Sales & Marketing
M: kristof.hots@waak.be
T: +32 56 36 34 34