How to achieve zero-defect production in HVAC cable assembly: Best practices
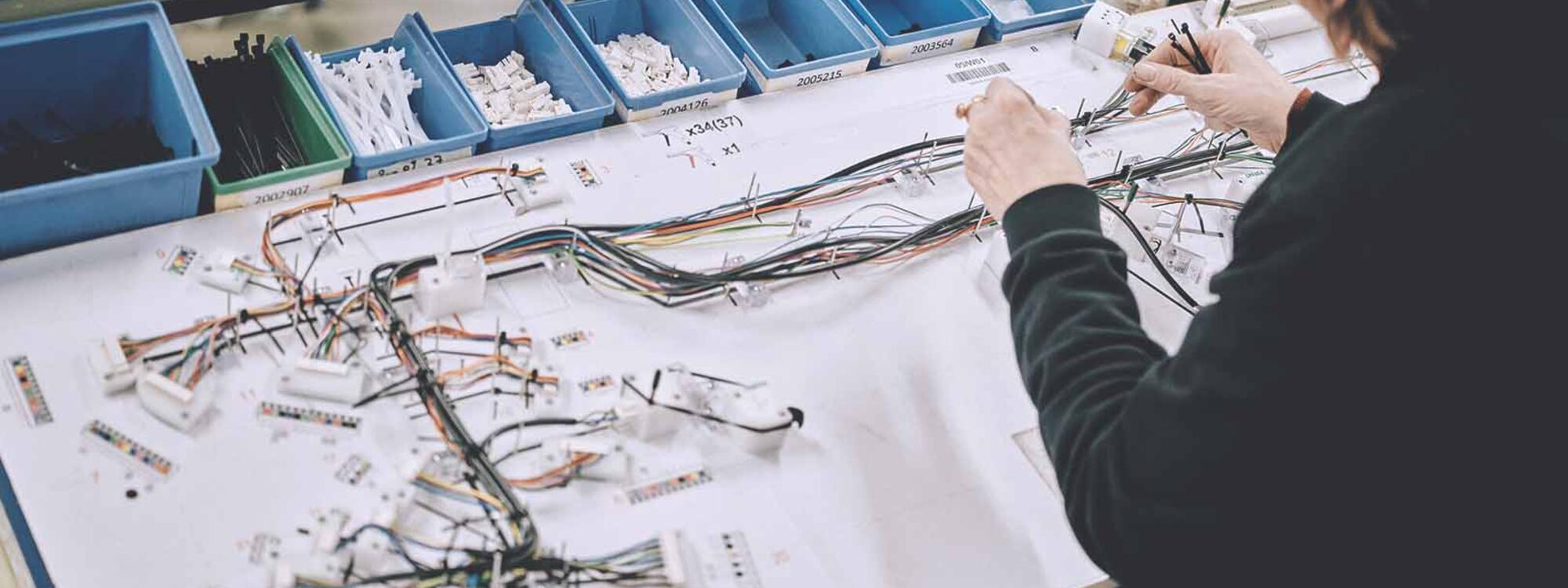
The HVAC market has become increasingly competitive and quality-driven. Products such as heat pumps, air conditioning systems, (heat recovery) ventilation systems have become more and more complex. In this context, zero-defect production has become the standard – not only to meet customer expectations but also to comply with today’s stringent safety regulations. As a long-standing supplier to major players in the HVAC industry, we understand that delivering premium-quality cables and cable harnesses requires more than technical know-how. It demands a quality culture of continuous improvement and a systematic approach to eliminating (potential) defects. This article serves as a best-practice case, detailing our approach to achieving zero-defect cable assembly production by highlighting the key principles, challenges and solutions.
What is zero-defect cable production in HVAC?
Strongly rooted in the First Time Right principle, zero-defect manufacturing is a quality management concept that focuses on preventing defects rather than detecting them after they have occurred. It aims to improve product and/or service quality, while reducing the costs associated with defects and waste. The ultimate goal of this philosophy is to create a production environment where defects are virtually non-existent, thereby minimizing waste, increasing efficiency, and consistently delivering high-quality to the customer.
Learn more about how you can achieve zero-defect cable production.
Challenges in achieving zero-defect cable and wire harness production
The aim of zero-defect production is clear ; however, the path to achieving it is more complex. At WAAK, for the assembly of cables and wire harnesses, we have identified 3 major challenges.
2.1. Managing a complex cable and wire harness manufacturing process
Cable and wire harness assembly involves a multitude of sequential steps - each of which must be executed correctly to avoid defects in the final product. In order to manage this complexity, WAAK has implemented the following measures:
Coherent process flow
For each wire harness, we create a comprehensive production file. Visualized through a ladder diagram, this file clearly displays the logical process flow. The diagram shows how the cable harness should be assembled to form the final product. This approach ensures that everyone involved understands the individual steps and how they are connected.
Workflow transparency
To make work less complex and to keep quality control at all times, we divide the production workflow into clearly defined operations. Each operation may contain several individual processes, all of which are documented with the following key information:
- Required tools and materials
- Workstation specifications
- Skill level of the operator
- Detailed process instructions
This structured approach ensures that we maintain an overview over the production flow at all times and that each step in the process is transparent and reproducible.
Visual Support
Finally, to further prevent errors, we make sure that each operator is provided with visual aids such as diagrams, photos, and instruction sheets. These tools offer the operator clear, step-by-step guidance.
2.2. Quality control in HVAC cable and wire harness production
Through preventive measures, clear standards and continuous monitoring, quality control is at each step of the production process:
Inspection of incoming materials
To control all incoming materials used in the production process, we have defined a clear set of specifications that must be verified upon delivery. If the delivered materials meet these specifications, they are accepted and registered. If not, the supplier is notified, and the materials are quarantined in a designated warehouse.
Tool verification and release
Before a tool is deployed in our production environment, it is subjected to a controlled release procedure:
- Sample products are manufactured and verified against specifications.
- A release report is logged, and verified and released tools are visibly marked
- All tools are subjected to preventive maintenance to ensure consistent performance.
FMEA Control Plan
At the core of WAAK’s quality strategy is the use of a Failure Mode and Effects Analysis (FMEA). This methodology helps us to:
- Identify potential failure modes in products and processes.
- Assess the causes and consequences of these failures.
- Prioritise actions to mitigate risks.
The results of the FMEA analysis feed directly into a detailed Control Plan, which specifies:
- Critical process parameters
- Inspection methods and frequency
- Specific actions to monitor and control quality
The FMEA analysis and control plan ensure that risks are proactively managed.
Read the full article and discover more proven strategies for achieving zero-defect production:
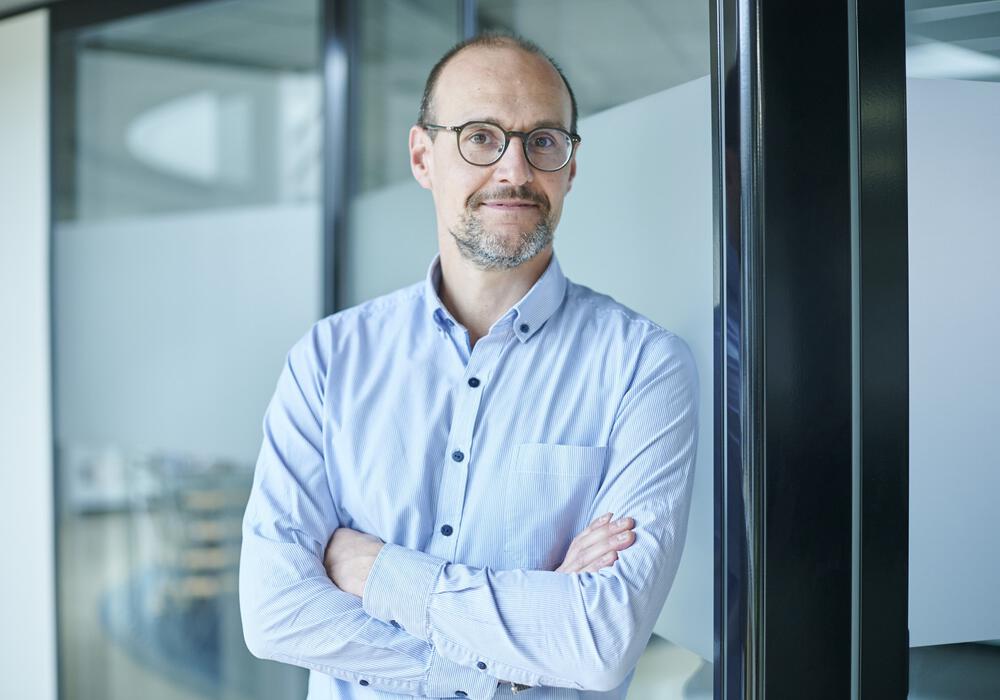
Don't look any further, we have all the expertise to help you out!
Kristof Hots
Director Sales & Marketing
M: kristof.hots@waak.be
T: +32 56 36 34 34