Overmoulding HVAC cables and wire harnesses: Benefits and challenges
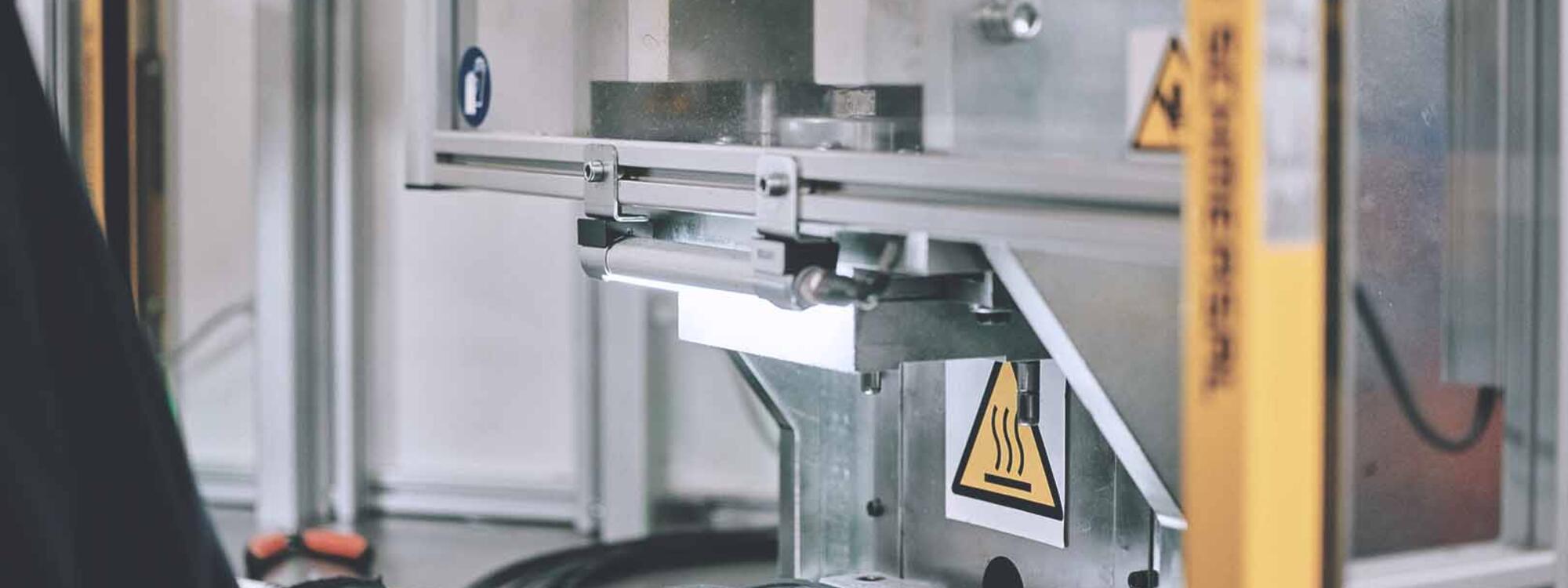
Overmoulding is an essential technique in the production of reliable and durable electrical components. It is widely used across various industries – especially in HVAC – where protection, mechanical strength, and aesthetics of cables, wire harnesses and connectors are crucial. This article provides an overview of the overmoulding process, highlights its advantages, and explains the key technical challenges and solutions associated with it.
What is overmoulding in cable assembly?
Overmoulding is a manufacturing process in cable assembly in which a cable, connector or cable harness is encapsulated in a protective plastic or rubber layer. Overmoulding offers many advantages:
- Protection: The plastic layer shields the connector from environmental factors such as dust, moisture, and mechanical stress, thus ensuring consistent performance.
- Mechanical strength: The process improves the mechanical robustness of the connection, increasing resistance to bending, pulling, and other mechanical forces.
- Reliability: Overmoulding reduces the risk of disconnection or damage, which enhances the overall reliability of the electrical system.
- Aesthetics: Overmoulding gives the cable, connector or cable harness a clean, professional and finished appearance.
Additionally, overmoulding can be used to create functional elements such as grommets. Grommets on cables and wire harnesses can serve as seals, feed-throughs, or strain reliefs, providing both mechanical protection and protection against environmental factors.
Want to learn more about overmoulding HVAC cables?
Technical Challenges in overmoulding HVAC cables and how to overcome them
While overmoulding offers numerous advantages, it also comes with specific technical challenges that require careful consideration. At WAAK Cable Assembly, we have the required expertise and technical solutions at our disposal to tackle these challenges and guarantee a high-quality end product.
1. Choosing the right overmoulding material: soft or hard plastic?
A key decision in the process is whether you should use soft or hard plastic. When it comes to hard plastics, you have to make an additional choice between high-pressure and low-pressure moulding:
- High-pressure moulding allows for highly accurate dimensions, with tolerances down to hundredths of a millimetre. However, this process is significantly more expensive than low-pressure moulding.
- Low-pressure moulding typically achieves tolerances within tenths of a millimetre and is cost-effective but it may lack the dimensional precision of high-pressure moulding.
What option should you choose then? Material selection primarily depends on the mechanical and environmental requirements of the final product. So, to make the right choice, it is important to consider all the relevant factors and seek expert advice.
2. Functional dimensions and mould design
To ensure that the overmoulded part meets the functional requirements, the dimensions must be carefully calculated, taking material shrinkage and tolerances into account.
At WAAK, we design our own moulds and, if necessary, we propose design adjustments to achieve the best possible result. This may require the creation of custom mould geometries, tailored to the specific application.
3. Risk of underfilling in overmoulding
An underfilled grommet can lead to poor sizing, loss of functionality, and compromised protection. To avoid this, the entire moulding process must be optimized: not only the mould design and material choice, but also the injection moulding process parameters such as dosage, holding force, speed, temperature, and cooling time.
At WAAK, the full injection moulding process is carried out in-house, and a strict quality release procedure is followed before production begins, ensuring that each product meets the quality standards.
4. Achieving optimal pulling force in overmoulded HVAC cables
One of the most challenging aspects of overmoulding is ensuring a strong pulling force, particularly when there is no natural adhesion between the overmoulding material and the cable.
For most applications, WAAK uses PA66 (polyamid 66), a high-performance thermoplastic polyamide specifically designed for low-pressure moulding. Its low viscosity allows the safe encapsulation of fragile components without damaging them. Additionally, it does not emit toxic fumes during processing and it offers excellent temperature resistance and adhesion to PVC cables.
When working with silicone cables however, you should take into account that they do not naturally adhere to PA66. So, we solve this by adding components to the cable to create a solid mechanical grip before overmoulding.
Read the full article to master the challenges and ensure optimal performance in HVAC cable overmoulding:
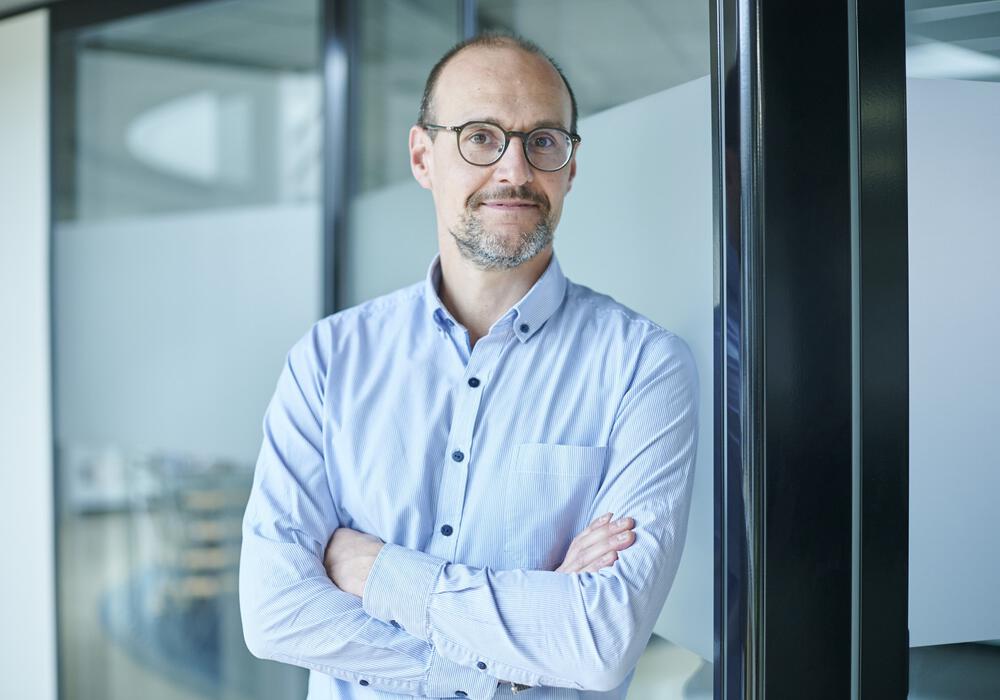
Look no further — we have all the expertise you need to support you!
Kristof Hots
Director Sales & Marketing
M: kristof.hots@waak.be
T: +32 56 36 34 34