Most common wire harness assembly mistakes in HVAC – and how to avoid them
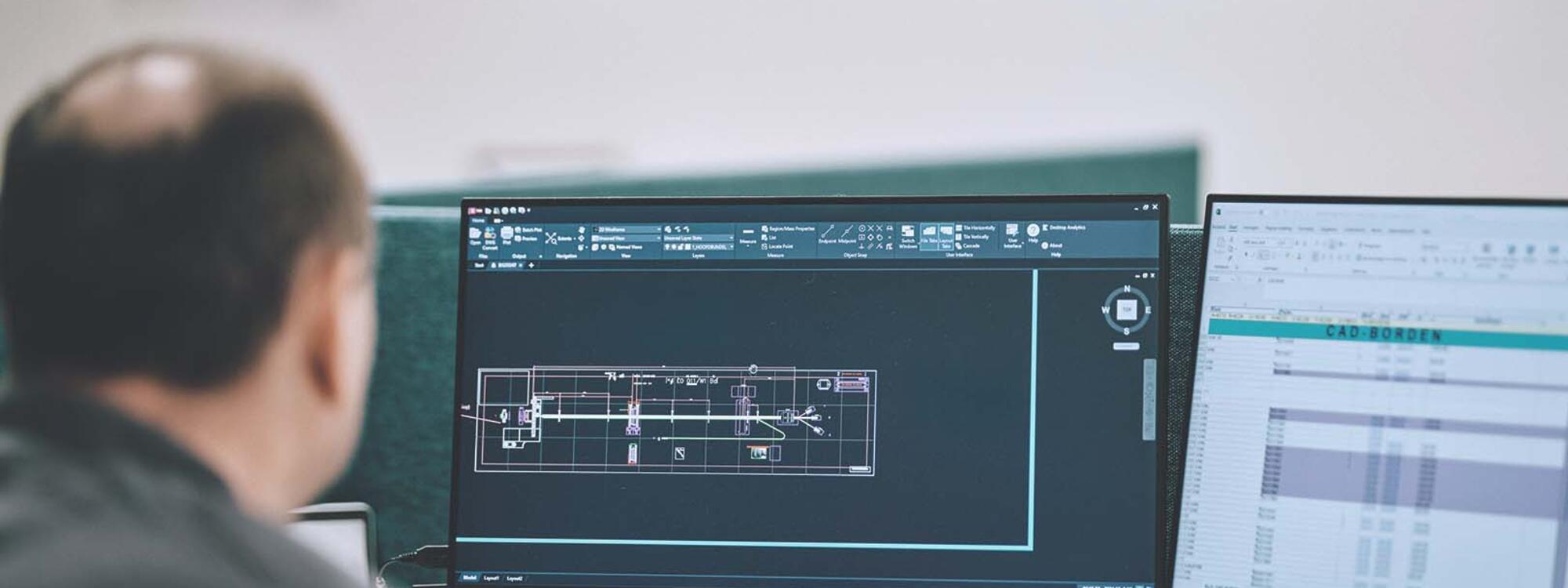
Cable harnesses are essential components of (electric) cars, HVAC applications, medical devices, and more. WAAK specialises in the assembly of wire harnesses for the HVAC-R industry. Assembling a cable harness is a critical process that requires know-how, precision, accuracy, and thorough quality control. In many sectors, a zero-defect standard applies due to safety regulations. This makes the implementation of stringent and systematic quality controls in the production process imperative. This article highlights the most common mistakes in wire harness assembly and explains how they can be prevented through proper design validation, tool selection, production monitoring, and systematic quality control.
What is a cable or wire harness? Definition, uses and HVAC applications
A wire or cable harness is an assembly of electrical cables or wires that are bundled together into an integrated unit. It organises and secures the cables and components, enabling the efficient transmission of electrical power and signals. In this way, a cable harness connects the various electrical parts and components within a device or system. Wire harnesses are commonly used in (electric) cars, HVAC systems, airplanes, medical devices, etc. WAAK is specialised in cable assembly for the HVAC-R industry (heating, ventilation, air conditioning, cooling and refrigeration).
Why component compatibility checks matter in wire harness assembly
At WAAK, before we approve a new wire harness design, we always perform a feasibility check to ensure that all the component combinations will work well together. It is not uncommon to discover incompatible cables and connectors, which can lead to potential design flaws.
To avoid these risks, WAAK always
- Evaluates all new component combinations before production.
- Creates samples and submits them to its quality department for thorough testing
-
Performs a feasibility check of the assembly process to identify possible issues, such as:
- Overcrowding of grommets with too many cables
- Inadequate pulling force due to poor material compatibility.
If we detect potential issues, we will propose alternatives to ensure the best possible outcome for the customer.
Essential tools for reliable wire harness production
Each component in a wire harness requires specific handling. To maintain consistency and quality, WAAK prescribes which tools should be used for each operation. We avoid hand tools to reduce human error and ensure repeatability:
- We use machines or semi-automated processes for maximum precision.
- We use tools that integrate multiple processes into one – for example: we use Komax Zeta machines, which combine wire cutting, stripping, crimping, and assembling.
How to validate wire harness designs before production
Cable harness designs evolve over time. To ensure that production follows the most up-to-date design specifications, you need a structured verification system that consistently checks and confirms that the correct version is being used.
At WAAK, we use several validations steps before we start production:
- Each order has to be scanned before the cable assembly can begin
- Checking the nail board to verify the correct layout.
- Checking the workstation setup to make sure it meets production standards.
- Evaluating the operator's skills to ensure that they can handle the specific assembly order.
This, however, isn't sufficient, do not forget the final steps, because they can truly make or break the final product... Curious about the final steps? You'll discover them in our whitepaper below.
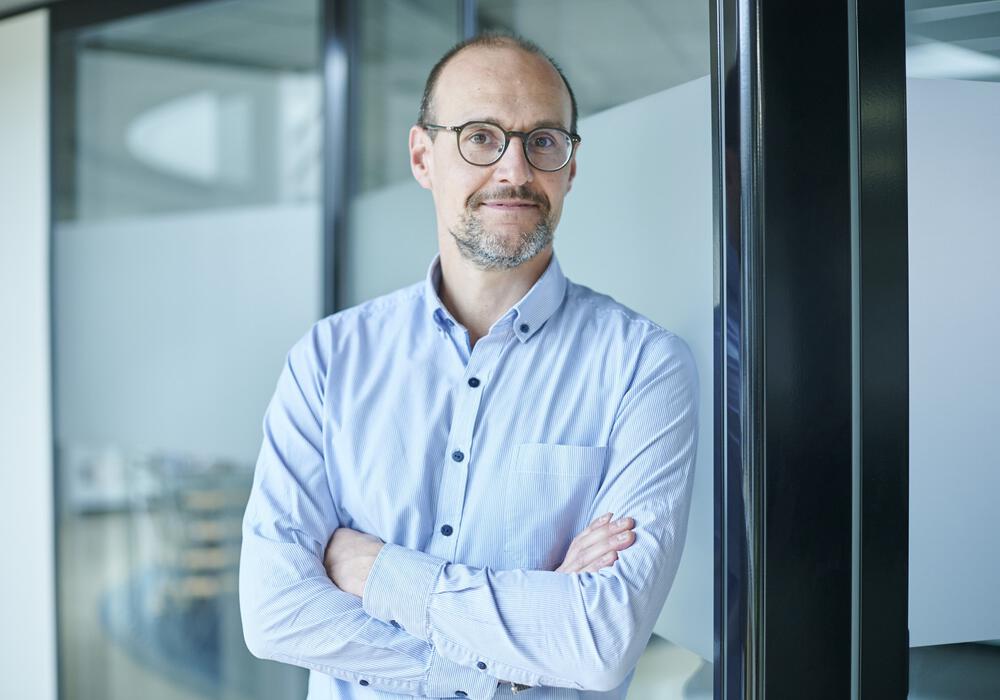
Don't look any further, we have all the expertise to help you out!
Kristof Hots
Director Sales & Marketing
M: kristof.hots@waak.be
T: +32 56 36 34 34